Subchapter 2.1
Risk assessment
Risk assessment or its documentation are often overlooked or missing which can cause problems when costumers or authorities ask to see the conformity documents. Some companies even regard this type of work and process as unnecessary work and a waste of time, so why is it important to have this documentation complete and ready to use?
Why should you do risk assessment?
The top three reasons to complete a risk assessment:
- In most countries it is required by law to conduct a risk assessment. In the EU, the Machinery Directive 2006/42/EC and the Machinery Regulation 2023/1230 require it.
- To be able to effectively design safety solutions tailored to workplace needs.
- We all want to avoid learning the hard way: accidents.
The key faults in risk assessment are the following:
- It is not completed in a structured way making it needlessly cumbersome.
- With new machinery it is done too late when the design is already mostly completed. This can make it extra challenging, time consuming, and potentially more expensive to implement sufficient safety measures.
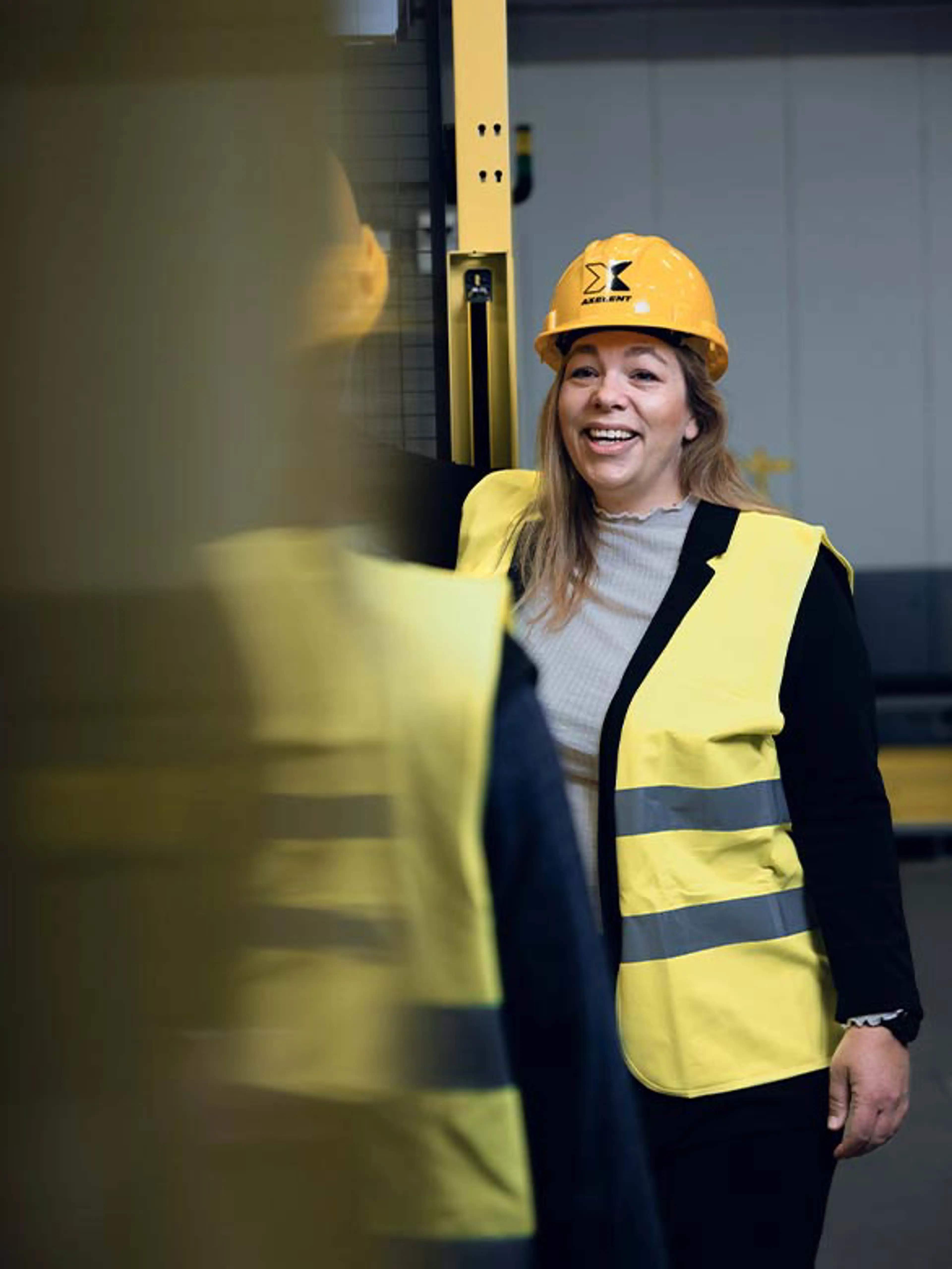
How to conduct a risk assessment by following a task-based approach
A requirement of (EN) ISO 12100.
Step 1 of 2
Follow a targeted, uncomplicated approach
- Identify the relevant phases of life
The relevant phases of the machine’s life (the so-called phases of life) are the different steps in the implementation and operation of a machine or process. These include for example transport, installation, regular operation, maintenance and troubleshooting. - Define operations and tasks
Define operations and tasks in those phases of life. An "operation" is an automatic process inside the machine. A "task" is an action taken by an operator. Typical operations and tasks in the operation phase for instance are: insert work piece (manually), start process, punch/mill/ grind/weld automatically, remove finished part from machine. - Identify hazards
Look for the hazards in each operation and task defined. For instance, punching automatically in a press can cause crushing, shearing and noise issues. To standardize risk estimation across operations and tasks, you should use a method such as the one detailed in the chart. - Estimate risk
Crushing in a press can cost a hand or arm. Large presses can kill a person. As a part of the workflow, parts or material must be inserted during each cycle, which causes the hazard to occur frequently. Since presses move fast, employees seldom have the chance to escape the hazard and are easily injured. - Select a safety measure
Select an appropriate safety measure to implement. Detail this measure like in the example chart. Find examples of safety measures under chapter 3.6 “Rules for safety switches” and chapter 3.7 “Monitoring systems”. - Check directive/standard
Check how the measure needs to be designed and to which laws and standards. This last step is the most difficult as it involves researching both standards and measures. You can find more information about this under chapter 2.2 “Researching standards”.
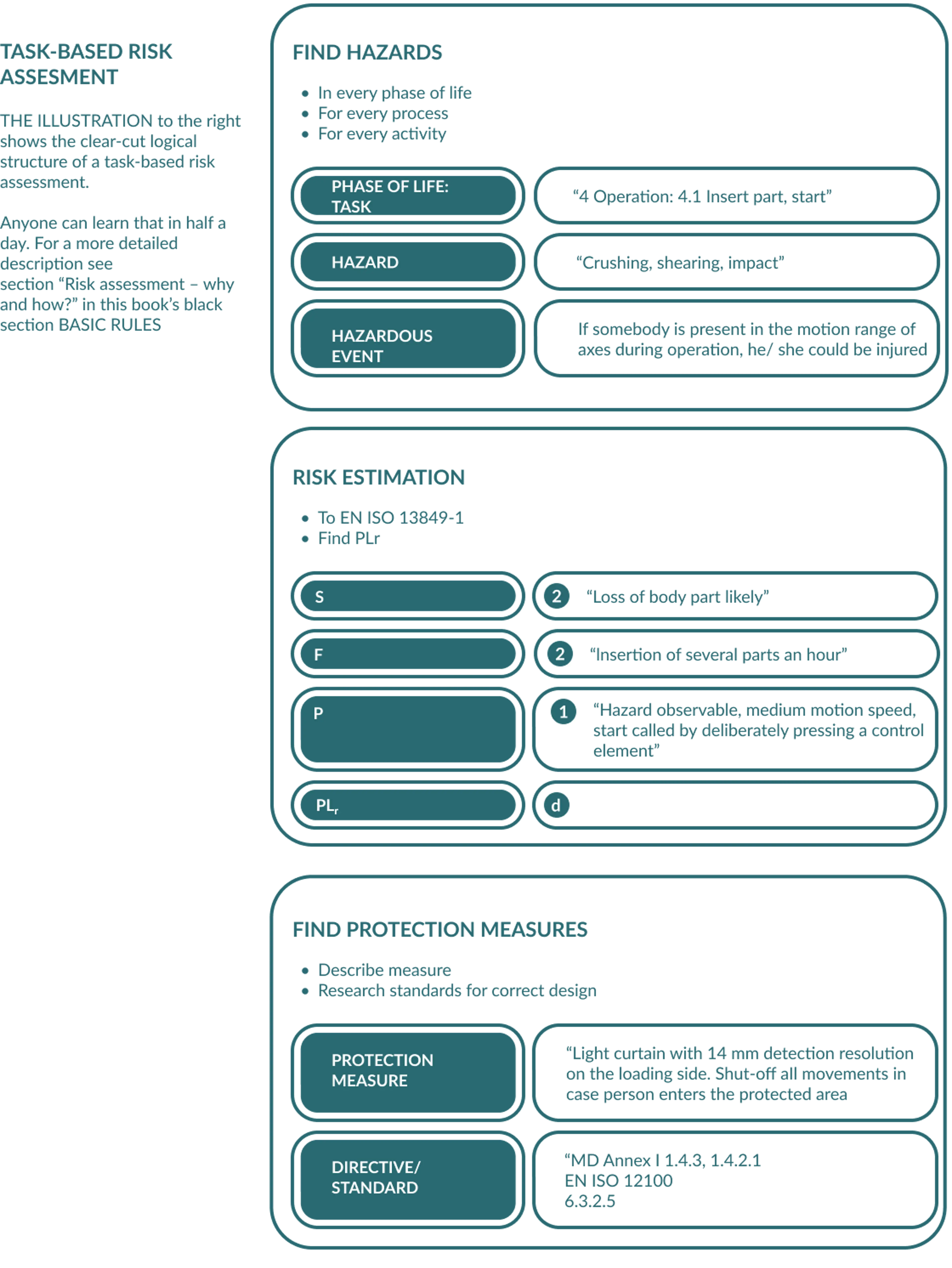
Step 2 of 2
Do it with time to spare
It is important to conduct the risk assessment well in advance before the machine is completed.
Performing the risk assessment while the machine is still “on paper" can help you detect hazards at an early stage. Although the very early design stages might be too soon, once you have a clear idea of how the machine will function and what moving parts are required, it is time to begin. The later you assess the risk, the more challenging, time-consuming, and less effective it will be.
Starting early will also help you avoid two common consequences of faulty risk assessment:
- Costly late design changes to accommodate sufficient safety features.
- Delays to final commissioning and operational use.
Although starting early is the best practice it is never too late to perform a risk assessment. It is vitally important that it is carried out, even if that results in the need for changes in the safety measures.
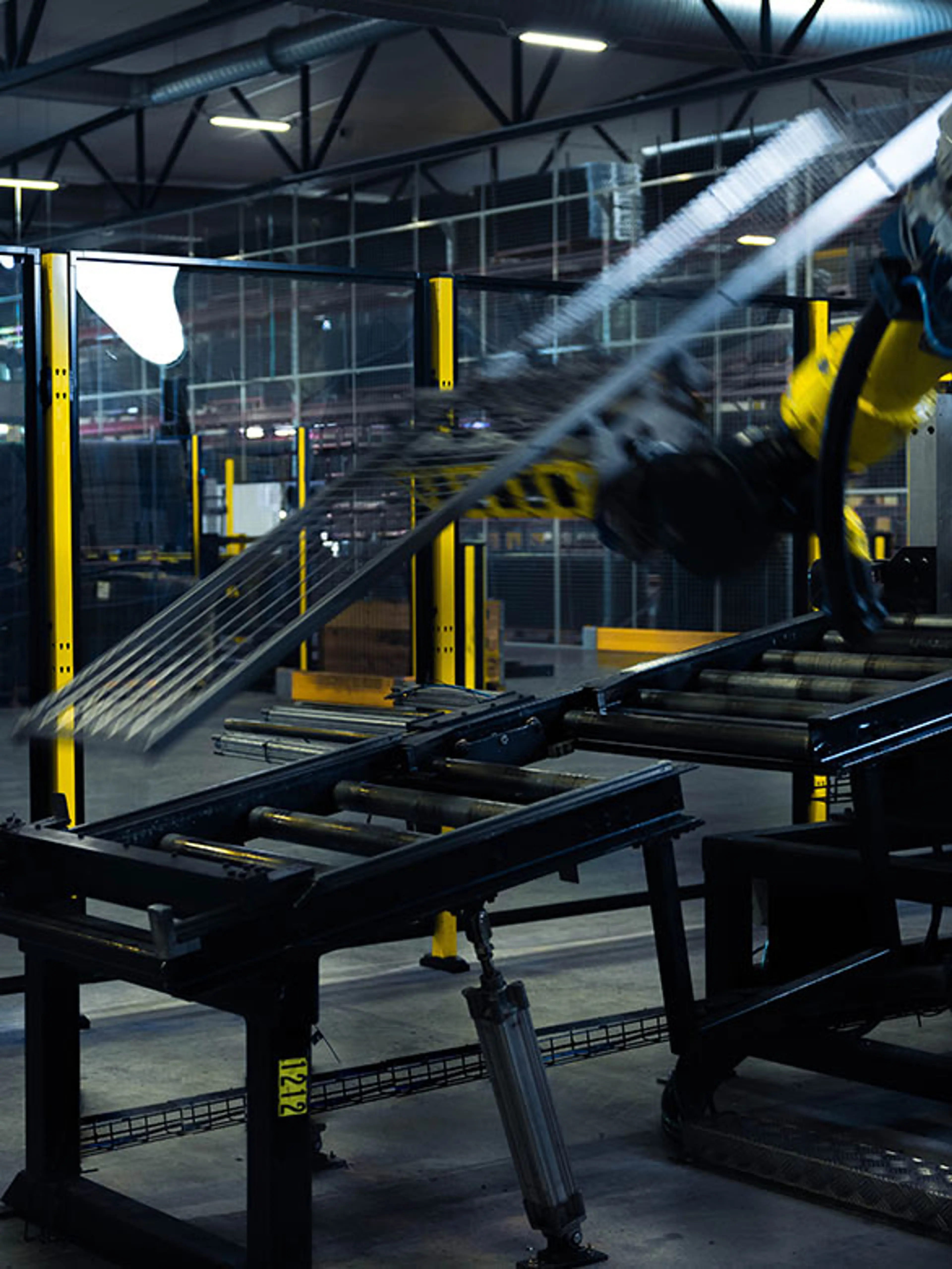
Follow a live risk assessment now
Define task to be assessed
Task:
Operator brings pallet into the machine and checks it.
Find the hazards and describe the hazardous event
Hazard
Approach of a moving element to a fixed part:
- Crushing, shearing
- Impact
Hazardous event
Operator may be crushed between moving robot and pallet or machine parts.
Select a safety measure
Type of measure:
Combination of guards and protective devices (llc).
- The hazard zone is enclosed by a guard fence that prevents intentional and unintentional access.
- A door is provided for access, which serves as a movable guard.
- The movable guard is provided with interlocking and guard locking that holds the door closed until robot and machine movements in the hazard zone have stopped.
- The machine cannot start as long as the door is still open or not locked.
- The door switch must be provided with an escape release lock.
Allocate requirements from directives/standards
Machinery directive:
- 1.3.7 – Risk related to moving parts
- 1.4.2.1 – Fixed guards
- 1.4.2.2 – Interlocking movable guards
EN ISO 12100: 2010: sections 6.3.3.2.2 and 6.3.3.2.3
Do a risk estimation to find the PL for the interlocking function
Do a risk estimation to find the PL for the interlocking function
S – Severity of injury: 2
Operator could be seriously injured by the robot, fatal injury possible.
F – Frequency and duration: 1
The pallet must be replaced approximately once per hour.
P – Prevention of harm: 2
The robot moves at speeds of up to 10 m/s, avoidance hardly possible.
O – Probability of occurrence: 2
No evidence available.
PLr: d
The most important parts of a risk assessment
Risk assessments is useful for several other processes, including development, manufacturing, testing and aftersales. Following is a list put together by Axelent containing the most important information to be included in a risk assessment report and the subsequent tasks depending on this information:
Join safety expert Matthias Schulz in this webinar on risk assessment. Learn practical strategies and expert insights to identify, analyze, and mitigate risks effectively. Important information for those aiming to enhance workplace safety and compliance. The webinar starts at the 2:00 minute mark.